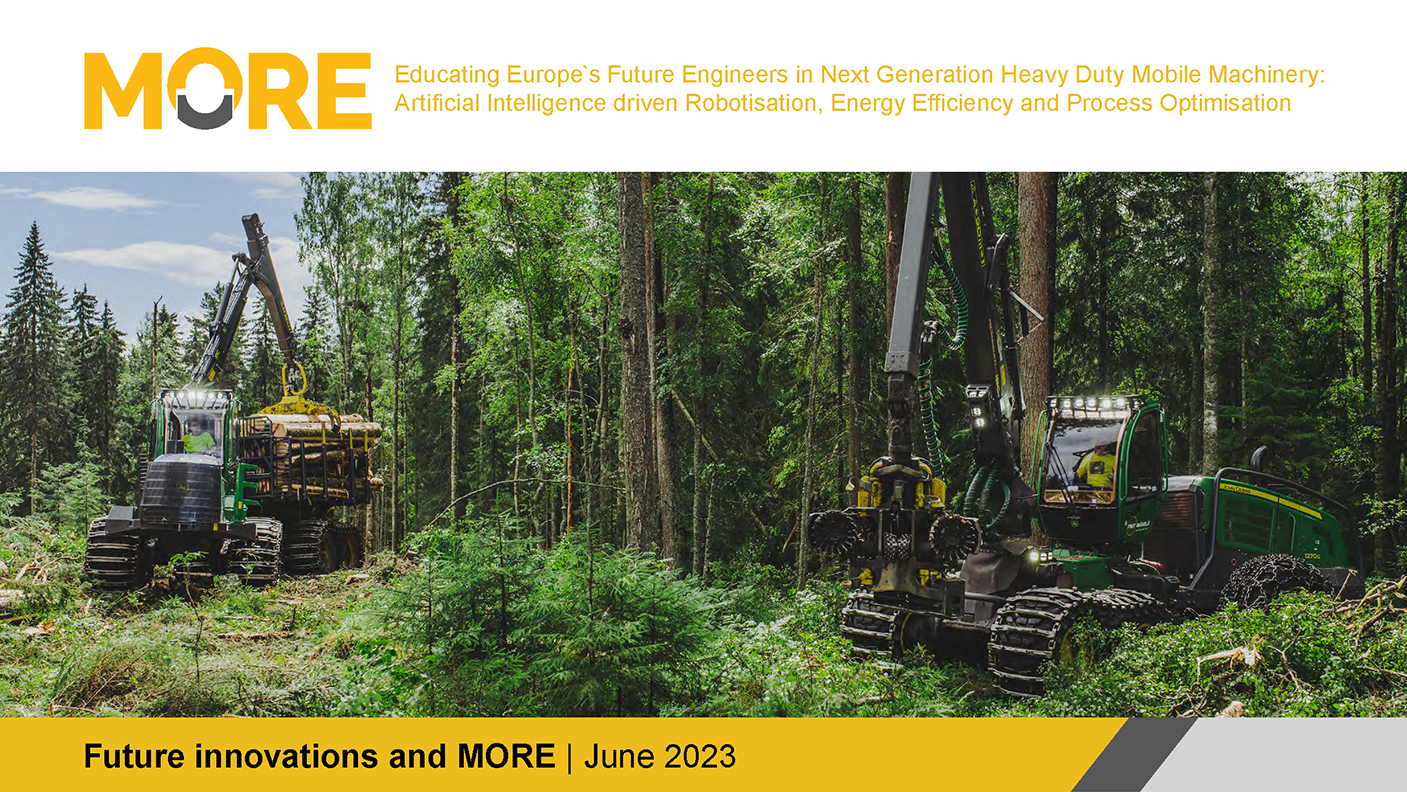
Automation and Control for Heavy-Duty Machines
Reshaping the future of operations with artificial intelligence and technological advances
Technology has taken a trampoline-leap in recent years, with the advent of machine learning algorithms, software, and hardware that have completely redefined the idea of “learning from data”. Outside the hype train related to large language models and simulated games, there is real potential to leveraging these machine learning tools to design intelligent control systems for the fleet of heavy-duty machines and robots. In this newsletter, we take a closer look into the usage of artificial intelligence for heavy-duty mobile machines (HDMMs). The first article describes how AI can be used for automating wheel loaders. The second article explains what can be leveraged from the machine learning world by engineers for more efficient and high-preforming machines in construction.
Articles
- Autonomous Wheel Loaders
What role does AI play? - Automatic Control for Heavy Duty Machines
Machine learning-based control systems for hydraulic loader cranes and wheel loaders
Autonomous Wheel Loaders
What role does AI play?
Wheel loaders are versatile machines and a key player on various work sites, they use different attachments such as buckets, forks, and other specialized tools to carry out different tasks. These include material movement where bulk material is moved from a pile to a truck or a hopper, pushing material into larger piles, and stockpiling, where material is dumped on top of a pile.
Jobs in the construction industry are becoming less attractive for the younger generation leading to difficulties in finding operators for Heavy Duty Mobile Machineries (HDMMs). One solution is to implement various autonomous functions, ranging from assistance systems to fully autonomous machines, where the operator coordinates multiple HDMMs without controlling them directly. This can reduce the number of operators as well as lowering the threshold for new operators to enter the job market by reducing the required operator education time using advanced assistance systems.
Automating wheel loaders also has the potential to increase efficiency and lower costs by optimizing work processes. The benefits are in the form of reduced fuel consumption and higher overall productivity. An autonomous machine has the advantage to operate during all the hours of a day, with the only downtime for refueling, recharging or maintenance work.
Artificial Intelligence (AI) is used to develop autonomous functions for HDMMs and for it to possible it needs different kinds of sensors, in the same sense as a human use different senses to operate the machine. The sensors are for example: cameras and lidars for vision and perception, pressure sensors for sensing the environment, and angle sensors to know the position of all the joints. These are then used for different functions necessary for autonomy such as: navigation, object detection, and pile loading. Lidars and cameras are used to create a local map of the surroundings that the HDMM can then use to localize itself and plan paths. Cameras can also be used to detect objects that the HDMM should avoid or find, as shown in Figure 2. The machine should for example avoid humans and other obstacles, and in the case of a wheel loader, it should also be able to detect trucks and other loading zones reliably. Finally, pressure sensors and angle sensors can be used for pile loading and controlling the wheel loader in general.
A popular AI method is machine learning (ML) where the behavior of the program is not determined by explicit instructions but by training on large amounts of data. Depending on the problem the type of data is different. In object detection the data consists of images of the different objects and their location. For pile loading the data consists of recorded bucket fillings by a human operator, where all the relevant sensors and joystick commands are logged. Our research in [1] uses machine learning to learn a pile loading controller which maps sensor inputs to output commands. The controller is able to load a gravel type of material with the similar performance as a human operator. We trained a controller capable of loading sand, gravel, and blasted rock by using the same methods as previously, with the addition of also using transfer learning to share knowledge between the different materials in [2].
In summary, AI is currently being researched to bring autonomous functions and assistance system to HDMMs including wheel loaders and has the potential to increase the productivity and lower fuel consumption.
About the author
Daniel Eriksson
Early Stage Researcher 6
Daniel is a 3rd year PhD researcher working on applying machine learning techniques for wheel loader automatization. His research focuses on the bucket filling process and how it can be optimized using different machine learning techniques on important factors such as loaded mass, loading time, fuel efficiency and reducing wear and tear.
Automatic Control for Heavy Duty Machines
Machine learning-based control systems for hydraulic loader cranes and wheel loaders
Classical control system design is a straightforward process: assume a system model and calibrate its parameters using system identification, then design and tune a controller that is both stable and performant. The theory of control and system identification more than often make simplifying assumptions such as linear models, controllers with few parameters, and so on, to make derivations possible. Machine learning bridges over this shortcoming, enabling any system to be fitted to a non-linear model using only data. Various models, including neural networks (feedforward, recurrent, convolutional, etc.) and non-parametric models are available nowadays for this use case. Our research in [4] showcases a model architecture and training workflow for learning accurate models of spool valve hydraulic systems (Fig. 3). The pressure levels in these systems can also be modeled, as our research in [5] proposes a data-driven modeling framework for predicting both working pressures in actuators as well as the pressure of a centralized supply pump (Fig. 4).
After modeling the systems with real data, it is possible to leverage machine learning to train high-preforming feedforward and feedback controllers. The aim of feedforward control is to improve accuracy and reduce the reliance of control and stress on feedback signals; this is done in a process called monotonic model-inversion, and the controller can follow any given joint trajectories [4] (Fig. 5).
Feedback controllers and transfer learning (from simulation to reality) can also be achieved using model-based policy optimization. This process trains a controller using trajectories generated from the surrogate models. Modern parallel processing hardware (GPUs, TPUs, etc.) are capable of parallelizing the training, reducing the training time to only a few minutes for our developed algorithm [6]. One of the enabling technologies in this regard has been the open-source automatic differentiation and optimization engine PyTorch [7] that has gone through rapid growth. We have seen promising results of applying these algorithms to real heavy-duty machines, such as wheel loaders (see our KnowMORE video in this link) and to loader cranes of different sizes (Fig. 6).
References
Header image courtesy of John Deere Forestry
[1] D. Eriksson, and R. Ghabcheloo. Comparison of machine learning methods for automatic bucket filling: An imitation learning approach. Automation in Construction, 2023
[2] D. Eriksson, R. Ghabcheloo, M. Geimer. Towards multiple material loading using transfer learning. The 18th Scandinavian International Conference on Fluid Power, SICFP’23, May30 -June 1, 2023, Tamperee, Finland.
[3] Yusheng Xiang, Hongzhe Wang, Tianqing Su, Ruoyu Li, Christine Brach, Samuel S. Mao, Marcus Geimer. KIT MOMA: A mobile machines dataset. IEEE Access, 2020
[4] A. Taheri, P. Gustafsson, M. Rösth, R. Ghabcheloo, and J. Pajarinen. Nonlinear model learning for compensation and feedforward control of real-world hydraulic actuators using gaussian processes. IEEE Robotics and Automation Letters, 2022.
[5] A. Taheri, R. Pettersson, P. Gustafsson, J. Pajarinen, and R. Ghabcheloo. Towards Energy Efficient Control for Commercial Heavy-Duty Mobile Cranes: Modeling Hydraulic Pressures using Machine Learning. The 18th Scandinavian International Conference on Fluid Power, SICFP’23, May 30- June 1, 2023, Tampere, Finland
[6] A. Taheri, J. Pajarinen, and R. Ghabcheloo. GPU-accelerated policy optimization via batch automatic differentiation of gaussian processes for real-world control. 2022 International Conference on Robotics and Automation (ICRA)
[7] A. Paszke et al. PyTorch: An imperative style, high-performance deep learning library. Advances in neural information processing systems, vol. 32, pp. 8026–8037, 2019.
About the author
Abdolreza Taheri
Early Stage Researcher 8
Ever since joining the MORE project in 2020, Reza has worked as a researcher at Tampere University in Finland and in Control Systems R&D at HIAB, Sweden. His research is directed towards deploying control algorithms on real loader cranes using machine learning. He has recently joined Volvo CE in Sweden to conduct research on automatic control for the newly developed fully electric wheel loader concepts.